1.引言
随着科学技术以及人们生活水平的不断提高,各种各样供大众娱乐、消遣的游玩设施日益增多;同时这些娱乐设施也更加复杂、多样、更具挑战性。传统的工法、技艺很难满足现在的精度要求。
在这种此消彼长的情况下,我们引用更加科学、以及非常成熟的三维精度管理技术,对此类结构比较复杂、制作难度相对较高的异形结构进行统一的精度策划、管理、制作;运用数字化模拟预拼装技术,对现场实际安装情况进行模拟,对后续现场安装可能造成的问题进行提前预防、整改。
2. 实施精度控制技术的目的及作用
精度控制技术最早运用在传统造船、海工平台等领域,经过多年的不断发展后,现已成长为一门成熟的精度控制技术,已经成功的运用在钢结构制作等各个领域,并且已经有诸多成功的案例。
通过钢构件制作前的精度策划,对各个类型的分段进行难点分析,对重点、难点分段可能出现的问题进行提前预防,以提高现场制作精度、降低成本消耗、提高工作效率。
通过钢构件制作过程中的精度控制,将各个分段制作过程中各个阶段进行定期检测,确保各个钢构建筑精度良好及安全使用,为后续安装打造良好的基础。
3. 钢结构精度控制技术:
通过钢构件制作后,进行数字化模拟预拼装,对现场安装情况提前预防,确保后续现场安装简单、高效做出有力保障。
钢结构在建造过程中精度控制技术方案是建筑钢结构件的一个重要内容,也是钢结构件得以顺利进行的重要保证。
3.1 精度策划
经过前期下发工艺,对各个类型的构件以及重难点、制作难度较大等构件进行统一管理,在早期通过前期工作累计进行一个初步判断,对可能发生的问题进行一个提前预防、重点关注、定期检测。
为了更完善后续的工作进展,对各种类型的构件统一要求、统一管理、统一检测。
例如:
组合类型名称 |
构件特点 |
示意图 |
单件管柱 |
现场安装不与其他管柱相连,可能有多个牛腿以及多个法兰,需要注意每个法兰的平面度以及角度,如果是有单个或多个牛腿的分段,需要注意各个牛腿之间相对的角度和与主管的角度。需要分别在焊前焊后进行测量,提前进行反变形加放以焊接收缩加放,防止焊后变形的问题产生,整体尺寸应控制在±2mm以内。 |
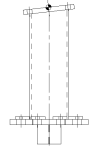
|
门式组合柱 |
由多件管柱组成,内部制作完成后需进行拼装,拼装后为门式组合。此类型组合分段需要注意与轨道连接法兰及地脚法兰的精度、整体拼接后各个管柱之间的档距。 |
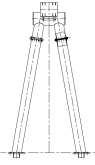
|
人式组合柱 |
由多件管柱组成,内部制作完成后需进行拼装,拼装后形式为人型。此类型组合分段需要注意拼装管柱的角度以及直线度。与轨道连接法兰及地脚法兰的精度、整体拼接后各个管柱之间的档距。 |
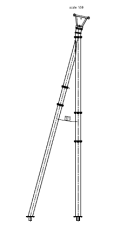
|
3.2 地样管理
构件制作前期,需要铺垫良好的基础-地样线,是一个构件制作的基准、以及初步检查的标准。把地样线精度控制在±0.5mm,经全站仪检测合格后打上样冲标记点,方便后续制作和检查。
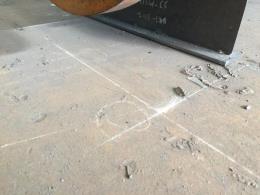
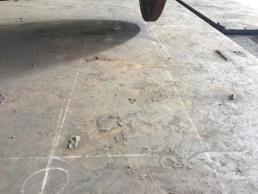
3.3 数字化测量技术
使用数字化三维检测技术,采用全站仪以及INCheck测量软件辅佐以精度管理流程实施,实现精度控制。根据构件检测需求,在相应的位置取点,使用与各个螺栓孔尺寸相对应的工装,分别对该构件各个位置进行取点。
通过坐标转换,将该分段现场局部坐标与其设计坐标相匹配,得到现场实制作结果与设计产生的偏差,从而更加直观的了解并发现问题。提高现场制作精度,提高了测量效率及测量数据的准确性和可靠性,大大减轻了现场制作时的工作量。
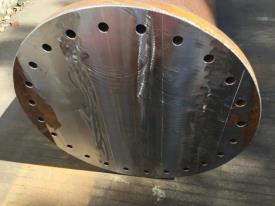
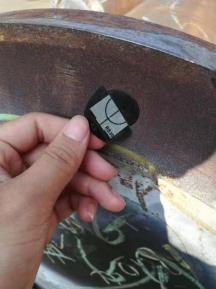
相比较传统的通过地样线、经纬仪、水准仪等检测方法,很难保证这种结构比较复杂、带空间角度等分段的角度的准确性。并且分解测量,存在累计偏差;比较依赖地样线,翻身焊接等问题很难保证精度良好。
而现使用的数字化测量技术,更加直观的体现现场制作时所产生的问题,最终提供更加全面的三维数据报表,如下图所示:
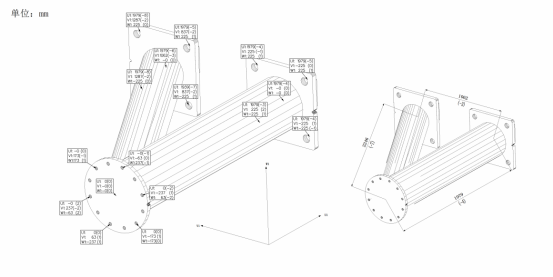
对此报告,制作现场可以更加方便的了解构件哪里出现问题,是否需要修正;可以更加准确的判断对后续现场安装是否有影响。
3.4 模拟搭载
为了确保在运输往安装地前,确保构件能顺利实现拼装,保证施工方的安装周期,在发运前,实施对构件的模拟拼装工作。其主要针对拼装数量较多,体积较大,在车间基本无法进行预拼装的情况,通过模拟搭载考察相邻构件之间的吻合度,以及和设计理论值之间的差异度。
以数字化测量为前提,通过虚拟技术和人工干预的应用,在电脑中将多个相邻构件进行模拟演示并分析得出有效的模拟预拼方案,在确保精度的情况下,指导现场吊装的一次定位完成。
模拟搭载使用流程:
①、将单构件测量的最终数据IN-Analysis文件分别导入IN-ASSEMBLY文件中,如下图所示:
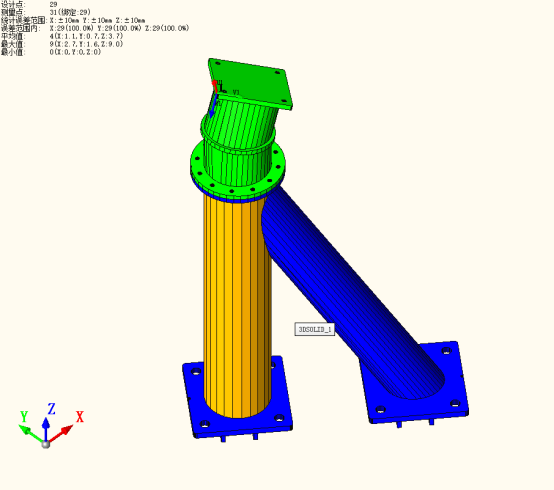
②、针对过山车类型的构件,我们主要将与轨道连接的分段设为基准分段,分别进行模拟搭载,通过我们的“IN-ASSEMBLY”模拟搭载软件,分别将需要搭载的分段进行实测点绑定,根据现场实际拼装情况,主要分为上下连接、前后连接、左右连接,根据需要搭载的分段依据现场拼接方向进行绑定,如图:该分段则需要上下对接绑定。
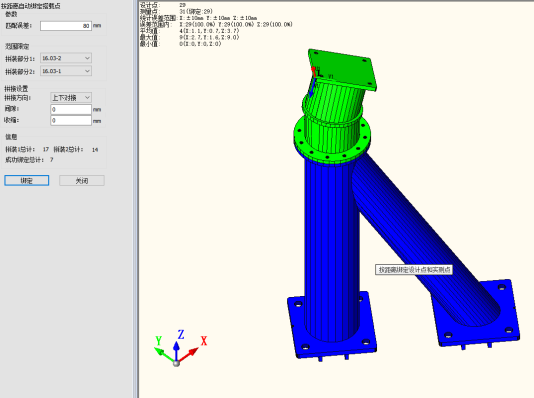
③、绑定成功后,我们则需根据绑定后的数据进行相应调整进行优化,最终出具报告,如下图所示:
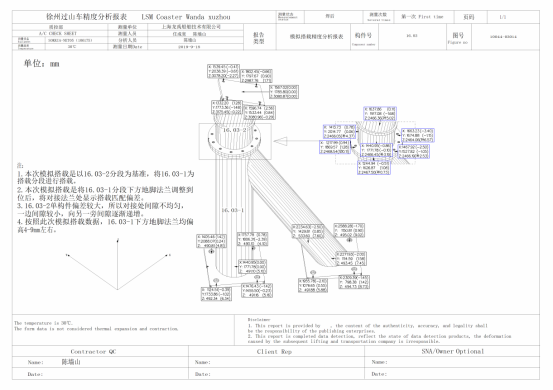
在该报告中,红色A框中为两分段连接处各个点位匹配的误差,对接方向为上下连接,如上所示,Z值处显示切0.1则为此处有0.1mm余量;Z值处显示补6.57则为此处有6.57mm间隙。红色B框中则针对该报告中的问题进行解答。由此出具报告进行提交,为后续安装提供有力的保障和建议。
4. 资源配置
精度管理配备 |
数量 |
备注 |
仪器 |
1、高精度索佳NET 05全站仪1台及三脚架等附件。 |
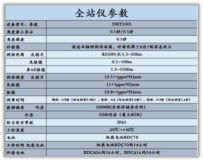
|
软件 |
1、IN-ANALYSIS分析软件1套。 2、IN-CHECK数据采集软件2套。 3、 IN-ASSEMBLY模拟搭载软件2套。 |

IN-CHECK IN-ANALYSIS 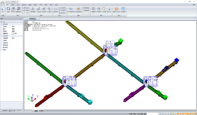
IN-ASSEMBLY |
工装 |
1、旋转标靶4~6个。 2、隐蔽杆1个。 3、反射标靶2个。 |
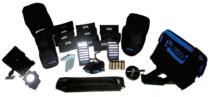
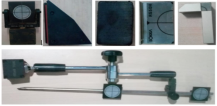
|
人员 |
本期项目共配置2人1组,每组精度测量人员2名。 前期只配置2组人员. |
|
5.结语
通过系统性的数字化检测介入及检测方式方法的改变,实现了制造方工人员精度意识提高、技能提高、检测作业标准化、数据可视化可追溯,确保了构件精度均保证在公差要求内,现场一次安装成功率近乎100%。在娱乐设施钢结构领域起到了至关重要的作用,为该领域后续高精度制造打造了良好的基础。