项目概述:
北京永定河大桥是一座全钢结构双塔斜拉刚构桥(详见图1),具有工程规模大、结构形式复杂、节点构造复杂、加工制作精度要求高、运输吊装能力要求高、测量测控精度要求高的特点,从加工制作到运输安装都极具挑战性。
预拼装是验证钢塔节段制造工艺、加工精度的重要环节。通过对本项目钢塔实体预拼装作业,模拟钢塔架设过程中匹配连接关系,尽早发现问题、尽早解决。
由于本钢塔断面尺寸大、线形复杂,采用实体预拼装难以实施,需要针对不同结构采用不同状态的预拼装作业。
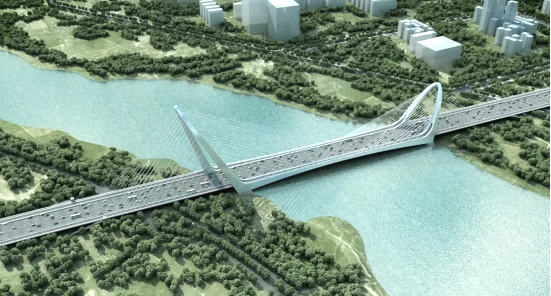
图1 现场规划图
1. 单节段精度监测
1.1 现场单节段检测
钢塔节段制造时需划设纵横基准线,肋板、腹板组装位置也均应划出相应基准线,节段位置交点敲好洋冲点,作为钢塔节段测量的基准。在塔柱安装前,在塔柱外侧壁板即现场三个方向布设好三组固定棱镜,用于后续安装订位监测;
如图2所示,现场使用0.5″高精度全站仪进行单节段检测,利用钢结构测量软件获取结构点及棱镜组的三坐标。
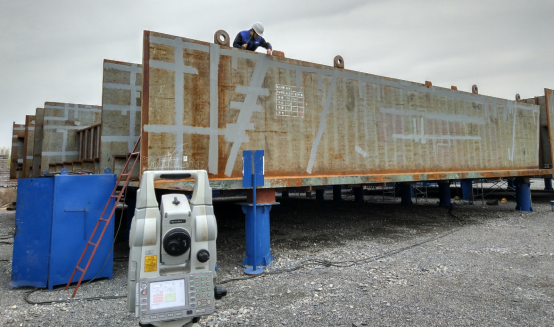
图2 单节段现场测量
1.2 单节段数据分析
本项目中共涉及三个坐标系:单节段测量独立坐标系;三维模型设计坐标系;现场安装坐标系(大地坐标系);单节段数据分析时将全部统一至现场安装坐标系下。
将现场采集的单节段坐标数据与转换后的模型设计数据进行匹配对比分析,分析原则为:
(1)添加现场理论轴心点;
(2)整体测量数据与理论数据初步分析;
(3)生成测量轴心点坐标,测量轴心点位置调整至理论位置;
(4)以单节段顶面为基准,进行平面拟合,包括平面与角度;
(5)基准面最佳拟合分析结束后,出具定位棱镜组大地坐标及轴心点位置指令报告A1;
(6)出具单节段尺寸偏差报告A2。
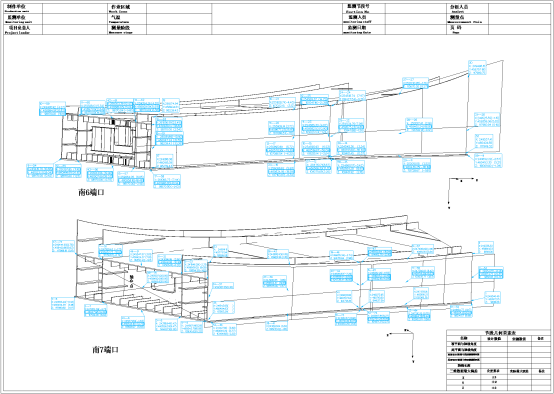
图3 单节段数据分析报表
2 模拟预拼装
2.1 预拼装目的
为了保证桥位架设精度、确定桥位安装基准、确保钢塔线形等,钢塔柱节段整体检测合格后,对钢塔节段进行实体预拼装和数字化预拼装。本项目钢塔节段进行预拼装的主要目的:
(1)验证钢塔节段接口的匹配性;
(2)检验钢塔柱制造整体线形;
(3)验证钢塔节段制造工艺的可行性;
(4)检验钢塔节段制造工装的可靠性;
(5)连接塔段间的临时匹配件及调整装置;
(6)塔段间加劲肋嵌补段的量配。
2.2 拼装数据分析原则
(1)获取现场安装后的对接面(节段顶面)大地坐标;
(2)以现场对接面实际位置为基准,与拼接单节段的测量结果进行对接分析;
(3)原则上不进行拼接节段的位姿调整;
(4)出具模拟预拼装报告B1,指导现场进行提前修整。
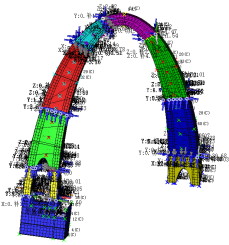
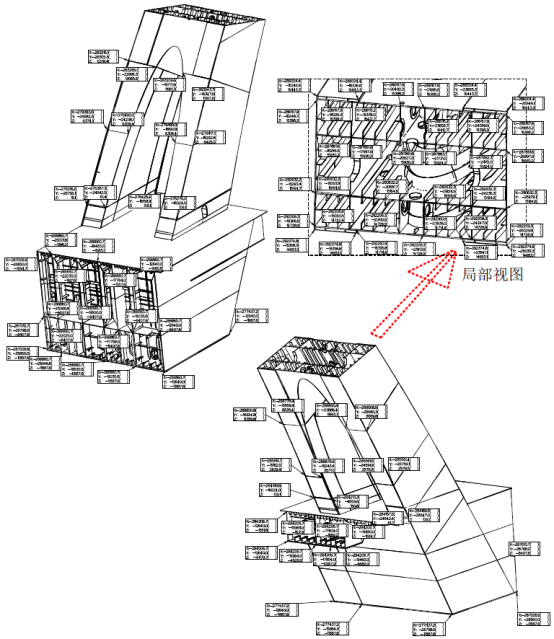
图4 模拟预拼装分析结果报告
3 现场定位安装
钢塔节段数量多,结构尺寸大、线型复杂,钢塔节段组拼在专用厂房内的组拼胎型上进行。
钢塔塔柱轴线的精度控制,是通过塔柱节段四周壁板上布设纵向基准线予以实现。钢塔节段制造过程中,每段四周壁板均需布设纵横向基准线,以基准线为基准进行结构的组装、预拼装等工作;在塔柱安装时,测量塔柱外侧布设好的三组棱镜,监测钢塔制造线型,如图5所示。
3.1 现场初步定位
现场吊装对接,根据模拟预拼装报告作出提前修正后,检查确认对接缝情况;根据节段上的基准点、线检查确认对点、对线位置偏移情况;通过拉尺和水准仪等方法确认节段拼装初期位置情况;
现场进行位置调整,直至结构面对接情况良好,加焊限位条,完成初步定位。
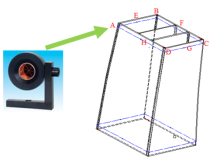
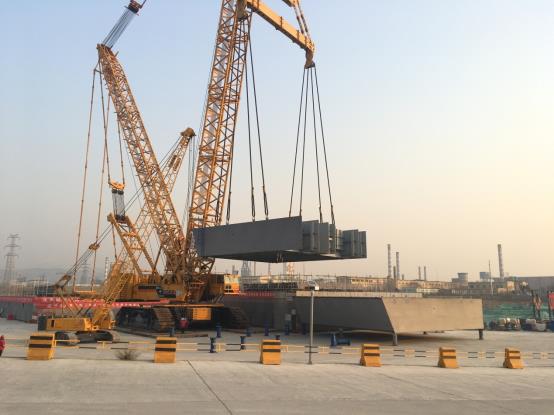
图5 现场吊装图
3.2 精确定位
如图6所示,现场布设控制网,坐标系统一至大地坐标系;控制点为浇筑的水泥柱加强制对中底盘,位置稳固不动。
将拼装节段位置三坐标拆分成平面(X,Y)与高程H,首先通过控制点的已知高程传递至基准段底脚,利用全站仪测距功能与电子水准仪结合完成向天顶的高程传递,进行拼接段的顶面高程测量,出具与理论位置高程的平面偏差报告C1,现场根据平面偏差报告C1进行高度调整,保证顶面高程满足安装规范限差要求。
全站仪架设在已知控制点上,通过联立控制网定向结束后,测量拼接节段上的三组棱镜平面坐标,与单节段测量出具的指令报告A1进行对比分析,指导现场进行平面位置的微调整,直至调整棱镜位置到指令报告A1下的坐标值。
拼装节段平面与高程坐标调整结束后进行拼装段的上平面位置复测,出具上平面及轴心点的位置、高程报告,确认是否满足安装规范要求并给出对应解决措施,保证下一拼装节段成功吊装。
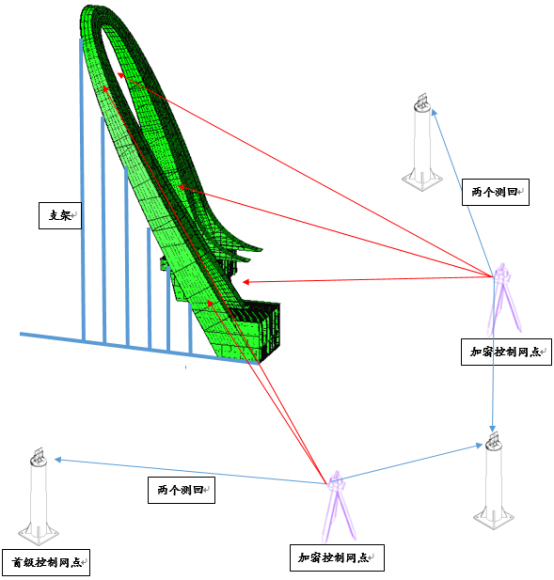
图6 现场定位示意图
4 总结
本文以桥梁塔柱钢结构模拟拼装为例,介绍了模拟预拼装的拼接目的与拼接原则;对数字化模拟预装的工程应用进行了较为充分的分析,基于模拟预拼装的特点,将其应用到现场钢结构安装以实现钢结构加工工厂制作与现场安装的互动。
目前,超高层、大跨度、结构复杂的钢结构建筑越来越多,造成一些钢结构构件越来越复杂,其安装控制难度大大提高;通过本项目的顺利实施,对于难以进行实地实物拼装的钢构件,利用数字化模拟预拼装技术可以作为一种有效的补充控制定位手段。